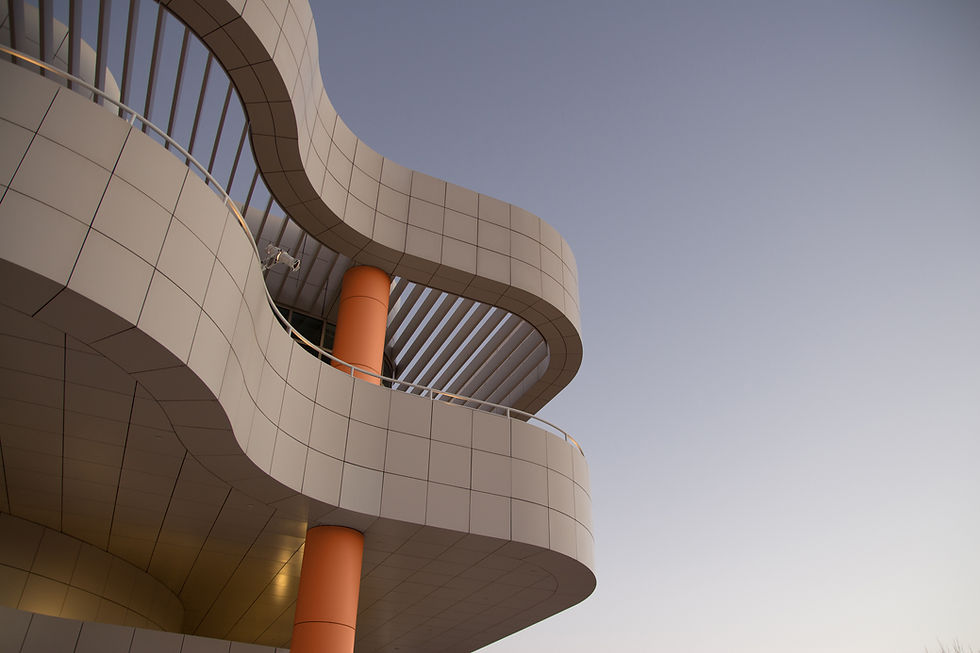
Cutting Costs with a Just-in-Time Inventory System: A Guide for Small Clinics
Oct 28, 2024
3 min read
In a small clinic, every dollar saved can be reinvested in patient care, equipment, or other essential resources. One effective method to reduce costs without compromising on quality is implementing a Just-in-Time (JIT) inventory system. Originally developed in the manufacturing industry, the JIT approach has proven beneficial in healthcare settings, helping clinics avoid overstocking, reduce waste, and save space—all while ensuring that essential supplies are always available.
This article will explore how a JIT inventory system works, why it’s so effective in healthcare, and how your clinic can implement it successfully to cut down costs.
What is a Just-in-Time (JIT) Inventory System?
A JIT inventory system is designed to keep inventory levels low by ordering supplies only as they’re needed. Unlike traditional inventory methods, where clinics maintain a sizable stock to avoid shortages, JIT aims to keep just enough on hand to meet immediate demand. Supplies are ordered more frequently, based on predictable usage patterns, reducing excess stock and minimizing waste.
For example: Instead of ordering a bulk supply of gloves or syringes that may sit on the shelf, potentially expiring before they’re used, a clinic using JIT would monitor daily usage rates and reorder these items only when inventory hits a low thresh
How JIT Lowers Costs for Clinics
1. Reduces Storage Costs
By keeping inventory levels low, JIT reduces the space needed to store supplies, freeing up valuable square footage for other uses, like additional examination rooms or equipment.
Stat: Clinics that reduced storage by 30% through JIT saved an average of $500–$1,000 monthly in space-related costs, such as storage cabinets and maintenance.
2. Minimizes Waste from Expired Supplies
In healthcare, many items have expiration dates. Overstocking increases the risk of supplies expiring before they can be used. JIT minimizes this by ensuring that only necessary items are stocked, reducing waste and associated costs.
Example: A clinic that switched to JIT inventory management saw a 20% reduction in waste from expired items, translating to savings of approximately $2,000 annually.
3. Improves Cash Flow by Reducing Large Upfront Purchases
Clinics often make bulk purchases to save on per-unit costs, but this can strain cash flow. With JIT, supplies are ordered as needed, avoiding large upfront costs and freeing up cash flow for other expenses.
Fact: A study by the National Institute of Health found that small clinics using JIT had a 15% improvement in cash flow, allowing for reinvestment in patient care and clinic improvements.
4. Enhances Supplier Relationships for Better Terms
Since JIT requires frequent ordering, clinics develop stronger relationships with suppliers, often gaining access to favorable terms like bulk pricing without bulk orders or even priority on high-demand items.
Insight: According to the Healthcare Supply Chain Association, clinics that communicate closely with suppliers under a JIT model reported a 10% cost reduction due to better-negotiated terms and timely access to needed items.
How to Implement JIT in Your Clinic
Analyze Inventory Needs and Patterns
Start by tracking inventory usage for a few weeks. Identify high-usage items (e.g., gloves, masks, syringes) and set “minimum stock levels” for each.
• Tip: Look for patterns in patient visits and seasonal trends that might affect usage. This helps predict demand accurately and avoid shortages.
Choose Reliable Suppliers
JIT depends on the timely delivery of supplies, so it’s essential to work with reliable suppliers who can fulfill orders quickly.
Action Step: Negotiate with suppliers for faster delivery times and explore options like standing orders, where deliveries are scheduled based on your clinic’s needs.
Use Inventory Management Software
Software systems can track inventory in real-time, alerting you when it’s time to reorder. This reduces human error and ensures you’re never overstocked or understocked.
Example: Small clinics using inventory management software reported a 25% reduction in manual inventory checks, saving valuable staff time.
Monitor and Adjust Regularly
JIT is not a one-size-fits-all solution, so it’s essential to monitor how it’s working and make adjustments as needed. Re-evaluate minimum stock levels every few months, especially during periods of high demand.
Pro Tip: Use key metrics, like average inventory turnover and order-to-delivery time, to measure effectiveness and adjust reordering practices accordingly.
Conclusion
Implementing a Just-in-Time inventory system in a small clinic can significantly cut costs, reduce waste, and improve cash flow, all while maintaining the availability of essential supplies. With careful planning, reliable suppliers, and the right software, JIT can transform how your clinic manages inventory. Start small, analyze your inventory needs, and adjust as you go to ensure a successful transition.
By adopting JIT, your clinic won’t just reduce costs—it will create a lean, efficient operation where resources are used optimally, allowing you to focus more on patient care and less on supply management.
